Identification of textile fabrics
Textile fabric identification can be mainly from three latitudes, textile fabric composition, textile fabric front and back, and warp and weft, textile fabric appearance quality, through the three major directions to identify, can help fabric buyers find good fabric at good prices. In the following, I will introduce the specific methods of the three categories of identification methods in detail.

Identification of the composition of textile fabrics
1. Sensory identification method
(1) Main Methods
Eye: use the visual effect of the eyes to see the luster, dyeing, surface roughness, and the appearance characteristics of the tissue, grain, and fiber.
Hand touch: use the tactile effect of the hand to feel the softness, smoothness, roughness, fineness, elasticity, warmth, and coldness of the fabric. The strength and elasticity of the fiber and yarn in the fabric can also be detected by hand.
Ear hearing, nose smell: hearing and smell are helpful to judge the raw materials of certain fabrics. Such as silk has a unique silk sound; all kinds of different fiber fabrics have different tearing sounds; acrylic and wool fiber fabrics have different smells, etc.
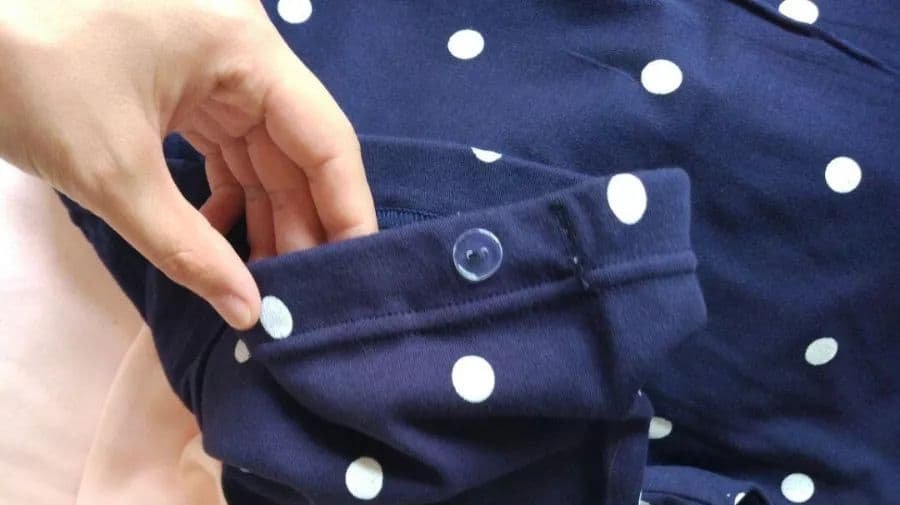
(2) Four steps
The first step is to initially distinguish the major categories to which the fibers or fabrics belong.
In the second step, the sensory characteristics of the fibers in the fabric are used to further determine the type of raw materials.
The third step is to make a final judgment based on the sensory characteristics of the fabric.
The fourth step is to verify the judgment result. If you are not sure about the judgment, you can use other methods to verify it. If the judgment is wrong, the sensory identification can be re-examined or combined with other methods for identification.
2. Combustion identification method
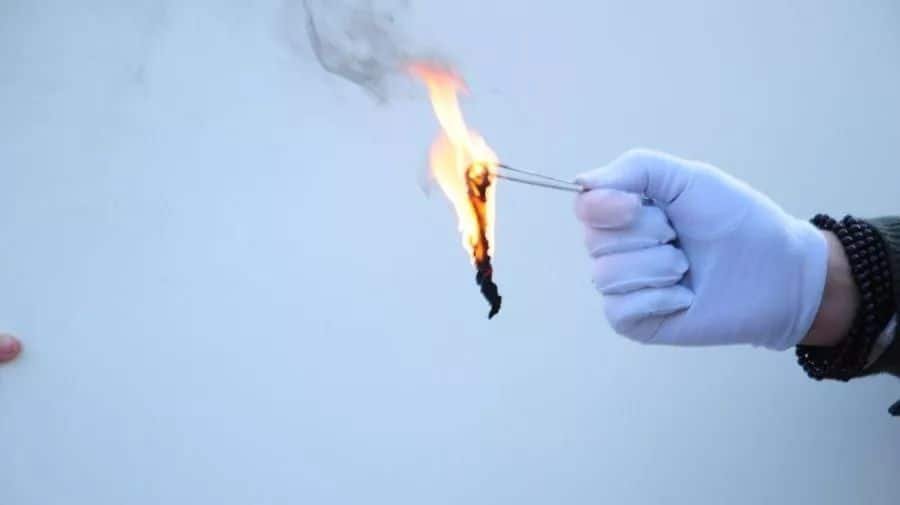
Burning characteristics of common textile fibers:
① Cotton fiber, fire is burning, burning speed, produce yellow flame, smell; slightly off-white smoke, can continue to burn after leaving the flame, blowing out the flame still has a spark in the renewal of combustion, but the continuation of time is not long; burning can maintain the original lint shape, hand touch easy to break into loose ash, ashes are gray fine soft powder, the charred part of the fiber is black.
② Hemp fiber, burning quickly, softening, not melt, not shrink, produce yellow or blue flame, with the smell of burning grass; leave the flame continues to burn quickly; ashless, light gray or white grass ash end-like.
③ Wool, contact with the flame does not immediately burn, first curl, then smoke, and then the fiber starts to burn; the flame is orange-yellow, burning slower than cotton fibers, leaving the flame immediately stop burning, not easy to continue to burn, with the smell of burning hair and feathers; ashes can not maintain the original shape of the fiber, but is the indefinite or spherical lustrous black-brown brittle block, with a finger crushed, the number of ashes is more, with the smell of burning.
④ Silk, burning more slowly, melt and curl, burned when shrunk into a ball, with the smell of burning hair; leave the flame with a slight flash, slow-burning, sometimes self-extinguishing; ash for the black-brown crisp small ball, with a finger pressure that crushed.
⑤ Viscose fiber, burning properties are basically similar to cotton, but viscose fibers burn slightly faster than cotton fibers, less ash, sometimes not easy to keep the original shape, viscose fiber burning will emit a slight hissing sound.
⑥ Acetate fiber, burning fast, with sparks, while melting, while burning, burning with a pungent acetic acid smell; leaving the flame, while melting, while burning; ash is black lustrous irregular block, can be crushed by fingers.
⑦ Copper ammonia fiber, burning quickly, not melt, not shrink, with the smell of burning paper; leave the flame continues to burn quickly; ashless, light gray or off-white.
⑧ Nylon, close to the flame caused by fiber contraction, contact with the flame, the fiber quickly curled and melted into a transparent gel, along with small bubbles.
⑨ Acrylic, while melting melt, while burning, burning speed; the flame is white, bright and powerful, sometimes slightly black smoke; similar to burning coal tar fishy smell or spicy smell; leave the flame continues to burn, but the burning speed is slow; ashes for the black-brown irregular brittle ball, easy to twist with fingers.
⑩Velon, burning fiber quickly shrink, slowly burning, the flame is very small, almost smokeless; when a large number of fibers melt will produce a large dark yellow flame, with small bubbles; burn with a special odor of calcium carbide gas; leave the flame to continue to burn, sometimes self-extinguishing; ashes for the black-brown irregular brittle beads, with fingers can be twisted to break.
⑪Polypropylene, while curling, melting, slow-burning; bright blue flame, black smoke, gel drops; smell similar to burning paraffin; leave the flame to continue burning, sometimes self-extinguishing; ashes are irregular hard lumpy, transparent, not easy to twist and break with fingers.
⑫ Chlorlon, difficult to burn; melting and burning in the flame, emitting black smoke; immediately extinguished when leaving the flame, not renewed; burning with an unpleasant pungent chlorine odor; ashes are irregular black-brown hard lumps, not easy to twist and break with fingers.
⑬Spandex, close to the flame first expanded into a circle, and then shrinkage melt; melt burning in the flame, burning speed is relatively slow, the flame is yellow or blue; leave the flame while melting and burning, slow self-extinguishing; burning with a special irritating odor; ashes for white adhesive lumps.
3. Density gradient method
The density gradient method of the identification process is: first configure the density gradient liquid, the configuration of the method is to mix two different densities and can be mixed with each other's light and heavy liquid appropriate mixture, generally using xylene as the light liquid, carbon tetrachloride as the heavy liquid, the use of diffusion, in the interface of the two liquids light liquid molecules and heavy liquid molecules diffuse each other so that the mixture in the density gradient tube to form a density gradient with a continuous change from top to bottom liquid. A standard density sphere is used to calibrate the density value at each height. Then the textile fibers to be tested are pre-treated by degreasing and drying and made into small balls, which are put into the density gradient tube, in turn, to measure the density value of fibers and compare with the standard density of fibers, so as to identify the type of fibers. Because the density gradient liquid will change with the change of temperature, it is important to keep the temperature of the density gradient liquid constant when conducting the test.
4. Microscopic observation method

By observing the longitudinal morphology of textile fibers under a microscope, it is possible to distinguish the broad categories to which they belong; by observing the cross-sectional morphology of textile fibers, it is possible to determine the specific names of the fibers.
5. Dissolution method
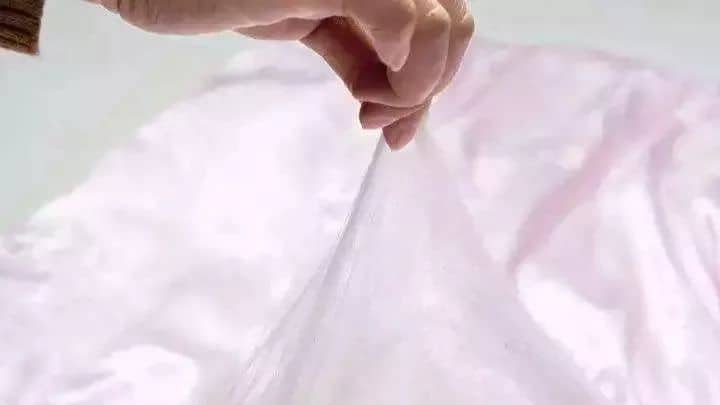
For pure spun fabrics, when identifying, a certain concentration of chemical reagent should be added into the test tube with textile fibers to be identified, and then observe and carefully distinguish the dissolution of textile fibers (dissolved, partially dissolved, slightly dissolved, insoluble), and carefully record the temperature when they are dissolved (dissolved at room temperature, dissolved by heating, dissolved by boiling).
For blended fabrics, the identification requires splitting the fabric into a single textile fiber, then placing the textile fiber on a slide with a concave surface, unfolding the fiber, dropping in chemical reagents, and observing under a microscope, from which the dissolution of component fibers is observed to determine the type of fiber.
Since the concentration and temperature of the chemical solvent have a relatively obvious effect on the dissolution performance of textile fibers, the concentration and temperature of the chemical reagent should be strictly controlled when identifying textile fibers by the dissolution method.
6. Reagent coloring method
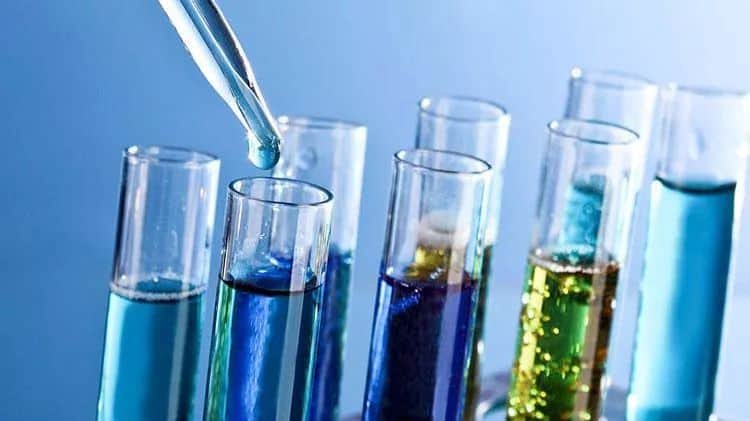
The reagent coloring method is a method to quickly identify textile fiber species according to the different coloring properties of various textile fibers to certain chemical reagents. The reagent coloring method is only applicable to undyed or pure spinning yarn and fabric. For colored textile fibers or textile fabrics must be advanced decolorization.
7. Melting point method
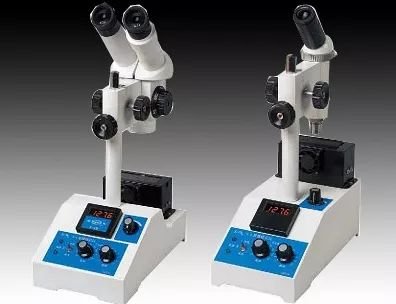
The melting point method is based on the different melting characteristics of various synthetic fibers, the use of a melting point meter to determine its melting point, so as to identify the varieties of textile fibers. Most synthetic fibers do not have an exact melting point, the same synthetic fiber melting point is not a fixed value, but the melting point is basically fixed in a relatively narrow range, therefore, the melting point can determine the type of synthetic fibers. This is one of the methods of identifying synthetic fibers, which is generally not used solely, but as an auxiliary method of confirmation after the initial identification, only with pure spun synthetic fabrics without anti-melting treatment.
Identification of the front and back side of textile fabrics and warp and weft direction
1. Identification of the front and back side of the textile fabric
It can be roughly divided into identification according to the tissue structure of textile fabrics (plain, twill, satin), identification according to the apparent effect of textile fabrics (printed fabric, sarong fabric, towel fabric), identification according to the pattern of textile fabrics, identification according to the edge characteristics of textile fabrics, identification according to the apparent effect of textile fabrics after special finishing (pile fabric, double-layer fabric, rotten fabric), identification according to the trademark and seal of textile fabrics, identification according to the packaging form of textile fabrics.
2. Identification of the warp and weft direction of textile fabrics
It can be identified by the fabric edge of the textile fabric, the density of the textile fabric, the raw material of the yarn, the twist direction of the finished yarn, the structure of the yarn, the sizing situation, the reed mark, the density, twist direction and twist of the warp and weft yarn of the fabric, and the stretchability of the fabric.
Identification of the quality of the appearance of textile fabrics
1. Textile fabric defect identification
The defects of textile fabrics include broken warp, sinking yarn, jumping flower, open edge, spider web, broken hole, thick yarn, bamboo yarn, big belly yarn, double weft, tightly twisted yarn, uneven strip, thin get, thin weft, thin section, dense road, thick section, side defects, cotton knot impurities, stains, color stripes, cross-file, off weft, hundred feet, folding, rolling shuttle, tawdry damage, wrong weft, loose warp, reed road, a reed through the wrong, narrow width, twill reverse, the pattern does not match, color difference, color stripes, stripes, stripes, the pattern does not match, deep and shallow fine point, skew, printing bias, desizing, color flower, staining these defects, according to the appearance characteristics can be identified.
2. Identification of deteriorated textile fabrics
The main method is to see, touch, hear, smell and lick.
Look, observe the color and appearance of the fabric, there is no trace left by the deterioration. Such as wind stains, oil stains, water spots, mold spots, staining, discoloration, or fabric normal different characteristics.
Touch, hold the fabric with hands, feel whether there is stiffness, moisture sticky, hot, and other symptoms of deterioration.
Listen, by tearing the sound of the fabric and the normal fabric occurrence of the crisp sound, such as sound dumb, cloudy, no sound, may occur when the deterioration.
Smell, by smelling the fabric, to distinguish whether the fabric deteriorates. In addition to the special finishing fabrics (such as coated with a rainproof agent or treated with resin, etc.), where there is a strange smell, such as acid, mold, bleaching powder smell, etc., it means that the fabric has deteriorated.
Lick, through the tongue after licking the fabric, such as flour moldy or with a sour taste, indicating that the mold has been moldy.
Learn these methods, it is not fabric rookie, identify the fabric that is a matter of minutes.