Shaping is the main process of finishing. Knitted fabrics through the mechanical action of the shaping machine and chemical reagents to prevent shrinkage, softening, hardening, and other effects, so that the fabric to achieve a certain shrinkage, density, feel, and can achieve the door width neat and uniform, smooth lines, clear pattern appearance effect.
The three elements of stentering and shaping
1.1 Temperature
Temperature is the most important factor affecting the quality of heat settings.
Because of the fabric after heat setting, the original existence of wrinkles are eliminated, the degree of surface flatness improvement, the size of the fabric thermal stability, and other taking performance have a close relationship with the heat setting temperature level.
1.2 Time
The setting time is another major process condition for heat setting. After the fabric enters the heating zone, the time required for heating and shaping can be divided into the following parts.
Heating time: the fabric into the heating zone, the fabric surface heated to the shaping temperature required time.
Heat penetration time: the fabric surface to reach the shaping temperature, so that each part of the fabric inside and outside the fiber, has the same shaping temperature required for heat penetration time.
Molecular adjustment time: after the fabric reaches the shaping temperature, the molecules in the fiber are adjusted according to the shaping conditions required time.
Cooling time: the fabric out of the drying room, so that the size of the fabric is fixed for the time required for cooling.
Usually refers to the setting time, often refers to the time required for the first three items, but does not include the fourth item. If the first item is regarded as a preheating effect, then the set time only refers to the time required for the second and third items, i.e., the time required for heat penetration and molecular adjustment.
Regarding the time needed for heating and heat penetration, it is determined by the performance of the heat source, the weight of the fabric per unit area, the thermal conductivity of the fiber, and the moisture content of the fabric.
1.3 Tension
The tension to which the fabric is subjected during the heat setting process has an effect on the set quality, including the dimensional thermal stability, strength, and elongation at the break of the fabric.
The warp dimensional thermal stability increases with the increase of warp overfeed during sizing, while the weft dimensional thermal stability decreases with the increase of door stretch.
The average single yarn strength of the fabric after sizing is slightly higher than that of the unstyled one, and the change in the weft direction is more obvious than that in the warp direction.
The weft direction decreases with the increase of stretching degree, while the warp direction becomes larger with the increase of overfeeding.
2 The main physical indicators that need to be controlled for sizing
2.1 Door width
The width of the door can be adjusted directly on the shaping machine during production. The adjustable door width on the shaping machine is in centimeters, while the company's order requirements are generally in inches, so in the production process, the inches need to be converted to centimeters before adjustment.
2.2 gram weight
In general, the gram weight is controlled by adjusting the overfeed. In the case of the rest of the tension remains the same, within a certain range, the larger the overfeed, the heavier the gram weight and the smaller the overfeed, the lighter the gram weight. Another door width and other tension changes will also cause changes in gram weight, but in general, these methods are not used to adjust the gram weight. (Overfeed compensation has some limitations)
2.3 Circulation
The loop is closely related to the gram weight and is the repeat size of the pattern from the starting point to the endpoint. Its control method is the same as that of gram weight. In general, the loop is controlled by adjusting the overfeed. With the rest of the tension constant, within a certain range, the larger the overfeed, the shorter the cycle and the smaller the overfeed, the longer the cycle. Another change indoor width and other tensions will also cause changes in the cycle, but in general, these methods are not used to adjust the cycle.
2.4 Shrinkage
Shrinkage is one of the most important physical indicators that need to be controlled for size. In general, the average shrinkage means the deviation of shrinkage in warp and weft direction is not more than 3%. For cloth with a particularly loose structure, the maximum deviation of shrinkage in the warp and weft direction can be 7%, but it must be confirmed by sales or customers before the production of large quantities.
By reasonable shrinkage, for new fabric, it means that the standard set according to the shrinkage test result must reflect GEK's production level, and for old fabric, it means that the shrinkage test result of the finished product must be within the deviation allowed by the customer's standard. There are many factors affecting shrinkage, including raw materials, knitting process, dyeing and washing process, sizing process, mercerizing process, gripping/grinding/brushing process and the operation of each process may affect shrinkage.
For shaping, the shrinkage is mainly controlled by resin or making a predetermined shape.
For cotton fabric species, shrinkage is generally controlled by the over-resin method. If the resin can fully react, the greater the amount of resin, the better the shrinkage, but the consequent problem is that the strength decreases more. Therefore, the amount of resin is subject to certain restrictions.
For fabrics containing stretchers and chemical fibers, shrinkage is generally controlled by the method of a predetermined type, assisted by the method of over-resin if necessary.
This type of fabric, the role of the predetermined type step is equivalent to the cotton fabric over resin step, to a large extent, determine the quality of the finished product, its importance is self-evident, must pay attention to. Another shrinkage is also related to the width, gram weight. Within a certain range, the wider the width, the greater the weft shrinkage and vice versa, the heavier the gram, the smaller the warp shrinkage, and vice versa, so to a certain extent you can improve the shrinkage by adjusting the overfeed and width. The warp and weft shrinkage of the fabric itself is also related. In the ideal situation, fabric in a certain state of warp, weft shrinkage, and the sum of a fixed value. Therefore, as long as no external tension is added, when the shrinkage in one direction becomes smaller, the shrinkage in the other direction will become larger. This is the guiding idea of making the shrinkage average. Of course, in the actual production process, it is impossible not to add external tension to the fabric. So must take measures in advance to improve. Such as rewash, over resin, etc. What specific measures to take the most appropriate, need to accumulate a certain amount of production experience to make an accurate judgment.
2.5 Distortion
Due to the twisting of the yarn, the yarn has a tendency to twist back after being woven into the fabric, forming a twist. The tendency to twist back is more pronounced in fabrics with a single-sided structure. The size of the twist is related to the twist of the yarn itself, the fabric structure, and the knitting process. The twist is generally controlled by diagonal sizing or stepwise sizing, and in many cases by a combination of both methods. However, for resinous fabrics, only oblique sizing can be used to improve the twist; for over-resinous fabrics, stepwise sizing can be used to improve the twist. When the amount of resin cannot be too large due to strong reasons or the fabric itself is too twisted beyond the adjustable range of the sizing machine, stepwise sizing cannot achieve the required twist, a combination of oblique sizing and stepwise sizing can be used to improve the twist.
2.6 Puckering
Pilling is related to raw material quality, fabric structure, resin reaction degree, and pre-treatment process. There are three main methods used to improve pilling.
1) enzyme washing; 2) over resin; 3) adding the appropriate amount of hard pulp in the material used.
2.7 Powerful
Strength is a physical indicator that cannot be repaired, so it should be carefully controlled during the production process. The size of the strength is related to the quality of raw materials, fabric structure, knitting process, the degree of resin reaction, and pre-treatment process. For sizing, the physical indicators of shrinkage, pilling, and twisting should be ensured while minimizing the damage to the strength. When these indicators cannot be taken into account, the strength is given priority.
2.8 Formaldehyde content
In general, high formaldehyde content is caused by an incomplete resin reaction. Generally, the formaldehyde content of adult clothing is <75ppm, and for some children's clothing and underwear, the formaldehyde content is <20ppm. as long as the resin reaction is sufficient, the formaldehyde content of adult clothing will generally meet the requirements. For children's clothing and lingerie single with strict requirements, as far as possible without resin finishing. If the resin must be passed in order to achieve other physical indicators, it can only be arranged to wash formaldehyde after passing the resin, and then wet setting.
2.9 PH
NIKE, TOMMY, and most domestic customers have strict requirements on PH value: light white PH range: 4.5-6.5. Therefore, for all clothes of these customers, we should pay attention to the strict control of PH value.
3 The relationship between each physical index and raw materials and processes
3.1 Relationship between raw material quality and each physical index
The quality of raw materials affects the grammage, width, strength, pilling, and twisting of the finished product. Under the same condition, the coarser the raw material, the heavier the weight, the wider the width, the better the strength of the finished product. The better the huggability of the raw material, the smoother the surface, the better the pilling of the finished product. This is more obvious in the fabric of grey yarn. The higher the twist of the raw material, the greater the twist of the finished product.
3.2 Relationship between the knitting process and each physical index
All other conditions are equal, the denser the yarn length, the heavier the weight (except stretched fabric), and the narrower the width, the better the strength and the less the distortion. Conversely, the more sparse the yarn length, the lighter the gram weight (except stretched fabric), and the wider the width, the worse the strength and the greater the distortion.
3.3 The effect of dyeing and washing method on each physical index
Generally speaking, other conditions being the same, the finished products of cloth dyed and washed in PD are narrower and heavier than those dyed and washed in YD or HD.
The width of the cloth is narrower and the gram weight is heavier.
3.4 The effect of dyeing and washing machine type on each physical index
Other conditions being the same, the finished product is usually narrower in width and heavier in gram weight than the cloth produced in an ambient temperature cylinder (cloth types with a large impact: 1X1, 2X2 RIB, WAFFLE, drawstring cloth, and cloths with a loose structure ……).
3.5 Relationship between finishing methods and each physical index
Finishing methods such as mercerizing, gripping/grinding/brushing, enzyme washing, and pre-shaping all affect the physical index to some extent.
Mercerization has a great influence on the finished result. For the same cylinder cloth, there is no comparable quality of the finished product when mercerizing or not mercerizing. After mercerizing, besides getting a better luster of the cloth, the structure of the cloth is much more stable than the original one, and the strength is also improved to some extent. The strength of the cloth is damaged to a certain extent by gripping/grinding/brushing and enzyme washing, and the grammage may be reduced. For cloths containing stretch and chemical fibers, the predetermined shape determines the quality of the finished product to a large extent. Temperature, speed, pattern, grammage, cycle, etc. must be strictly controlled, otherwise, the finished product may not meet the customer's requirements.
4 shaped door width and overfeeding determination
For the old fabric, the maximum width of the order can be converted into centimeters and set the direction for the fabric that does not need to be pre-shrunk, and the fabric that needs to be pre-shrunk can be widened by 2-3 inches on this basis. The overfeed is mainly decided according to the looseness of the cloth and the past production experience, and the overfeed of different cloths varies greatly. When the production is according to the set overfeed, under the machine gram weight, the cycle can not reach the requirements of the order, to be adjusted in a timely manner.
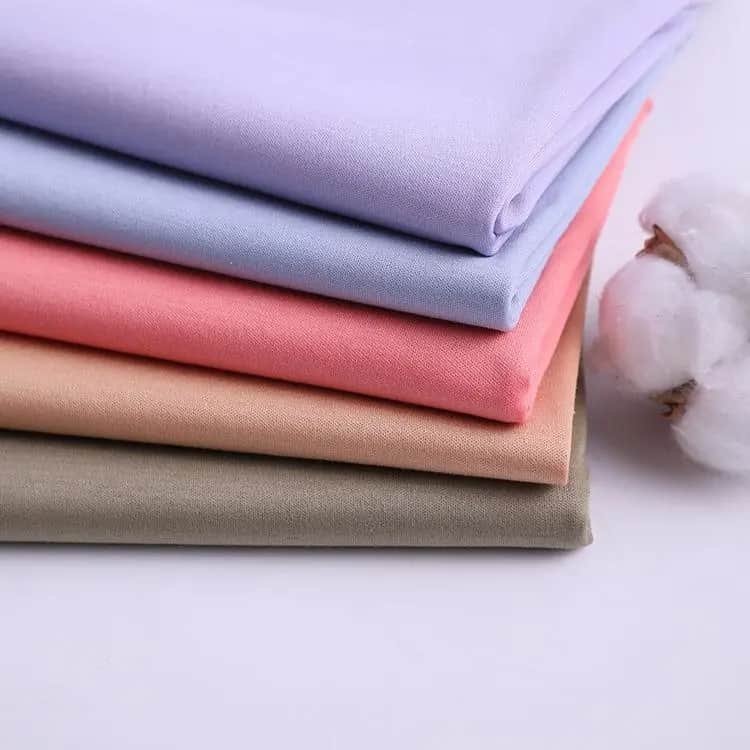
The overfeed of cloth with the mercerizing requirement is generally smaller than that of cloth without mercerizing; the overfeed of cloth with test method LINE DRY, HANG DRY, FLAT DRY is generally smaller than that of cloth with test method TUMBLE DRY. Cloths with linting before shaping are generally produced with a larger overfeed.